Danny Constantinis (Executive Chairman & CEO) EM&I Group, Malta.
Introduction
Following the downturn, pandemic, bankruptcies, amalgamations, and geopolitical turmoil, the drilling sector has finally ‘bounced back’ with thousands of new wells needing to be drilled.
According to the renowned Rystad Institute this increased level of drilling is needed to meet the future demand for hydrocarbons not only to transition into renewables but to meet the increasing demand for crude oil as the basic feedstock for a multitude of products until alternatives can be found.
According to their forecasts thousands of new oil wells will need to be drilled and hundreds of new oilfields brought into production to meet the demand. Also, the ‘just in time’ supply chain philosophy which worked OK before the pandemic will have to be replaced by a ‘just in case’ philosophy with more storage capacity and strategic reserves to cope with potential disruptions.
Keeping drilling assets operational with the minimum downtime or off hire time will be critical for efficient operation in future. This is where diverless and remote methods of inspection and maintenance will help, both to keep assets operational and to enable ‘warm stacked’ and ‘cold stacked’ assets to become operational swiftly and without downtime for class inspections.
Drillship utilisation is forecast to be up to around 85% and day rates are returning to pre-pandemic levels, so the future looks promising at the moment. The ‘hot spots’ for drilling are mostly in the ‘golden triangle’ in the waters off Brazil, Guyana, West Africa and the Gulf of Mexico.
EM&I’s robotic and digital asset integrity technologies have led the way…
Our robotic and digital asset integrity technologies have led the way to improving the safety, efficiency, and economy of inspection and repair as a result of our leadership of the HITS (Hull Inspection Techniques and Strategy) Joint Industry Project.
This has produced a number of ground-breaking ‘industry driven’ innovations including the ODIN© range of diverless underwater inspection and repair methods. These range from UWILDs (under water inspection in lieu of drydocking), inspection and repair of MODU hulls, valves, structures, sea chests, and mooring systems, with more than 200 projects successfully completed for many of the leading drilling companies throughout the world.
Our unique Integrity Class ROVs are fitted with a wide range of tools to tackle almost any task required and special thrusters to work at any angle. They are easily launched from the deck of MODUs or a support vessel using a specialised LARS (Launch and Recovery System) which enables them to be deployed through the splash zone safely.
Top Image Caption: Deck launching an ROV with a portable LARS
The use of backup UPS (uninterruptible power supply) units enables safe recovery in the event of ship power failure or instability and the development of specialised power systems improves performance in challenging currents and sea states – in short, these ROVs can operate in challenging sea conditions which would be either unsuitable or unsafe for divers.
A recent innovation is the ‘motorised’ LIMPET™ blanking plates which enables sea chests to be blanked off in any orientation without divers and without drilling downtime. These are tailored to fit the hull and are deck launched and remotely manoeuvred into position using lines attached to the sea chest by an ROV which then keeps a watchful eye on the process.
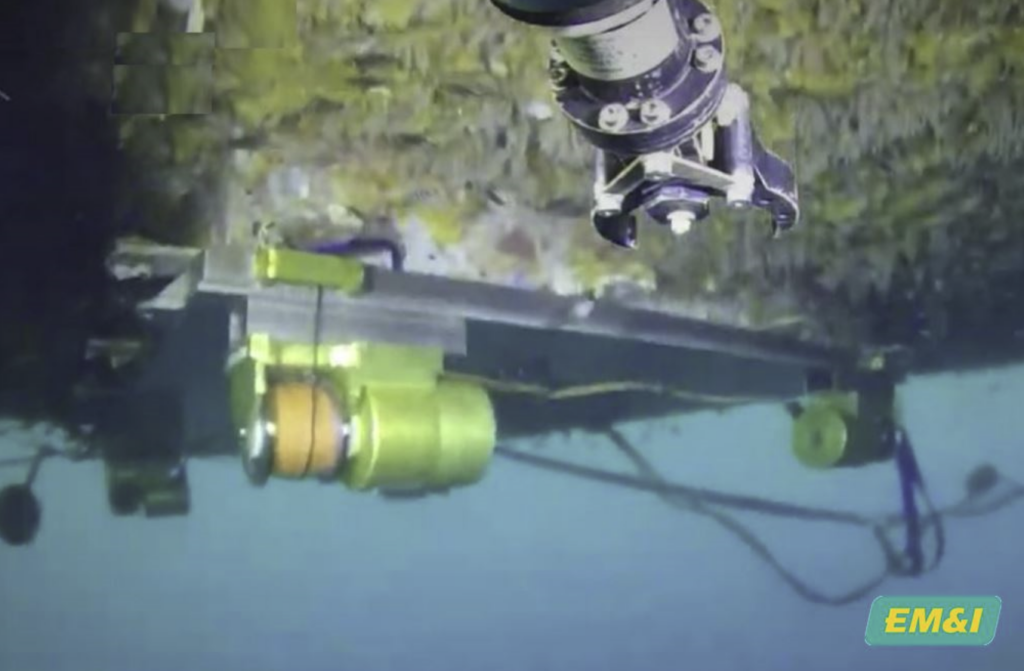
A further advance is the use of repair cofferdams, placed in location without divers, using customised ODIN access ports with winches which are attached to the inside of the hull. The winch lines are pushed through the ODIN access ports, retrieved by an ROV, and attached to the cofferdams so that they can be drawn onto the hull to create a dry working environment for the repairs. These have proved to be a significant advance over traditional methods using divers and can also be used for hull repairs a well.
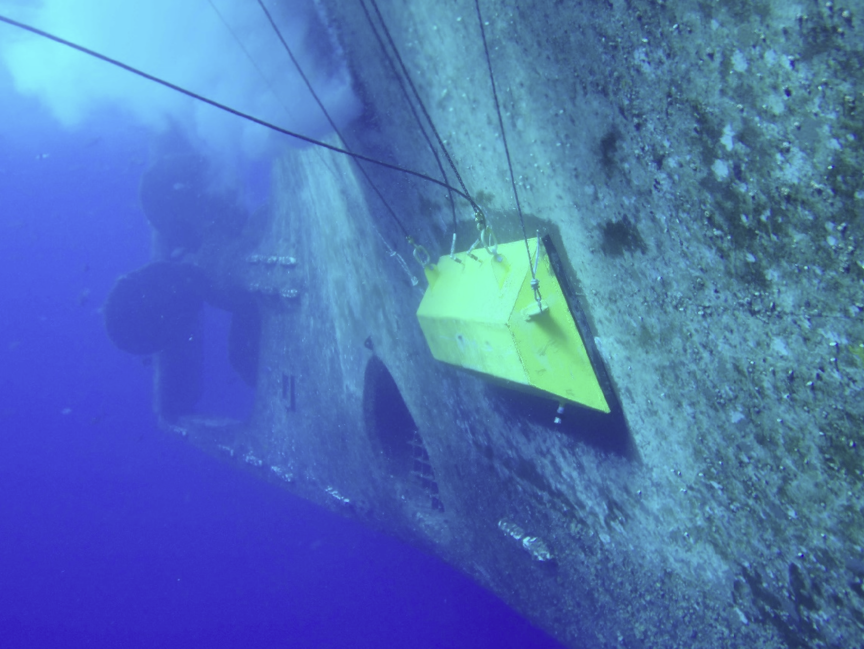
NoMan© is another ground-breaking technology – the use of combined synchronous laser scanning and optical cameras means that confined spaces such as tanks and pressure vessels can be inspected in a fraction of the time and cost than manned entry – the bonus being no safety risk of confined space entry or working at height. The NoMan equipment can be inserted through deck openings and used to scan tanks in great detail – sufficient to measure wall thickness and to detect any anomalies such as fractures, corrosion, and distortion. The data collected can be used to directly develop 3D and FEA (Finite Element Analysis) models to establish the remaining local strength of the structure. This can justify deferring or avoiding unnecessary repairs which can be costly and operationally disruptive.
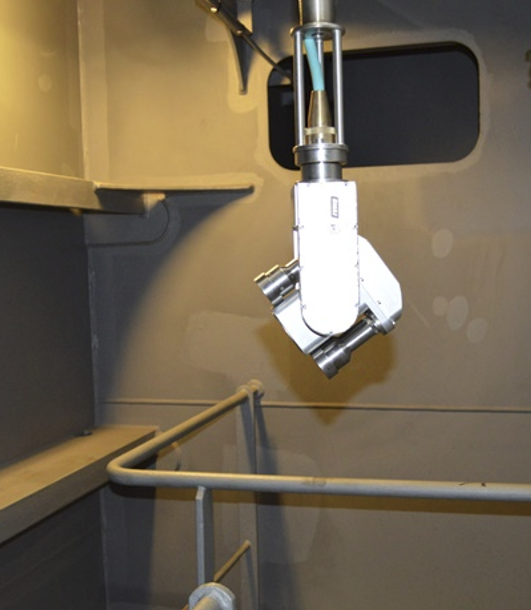
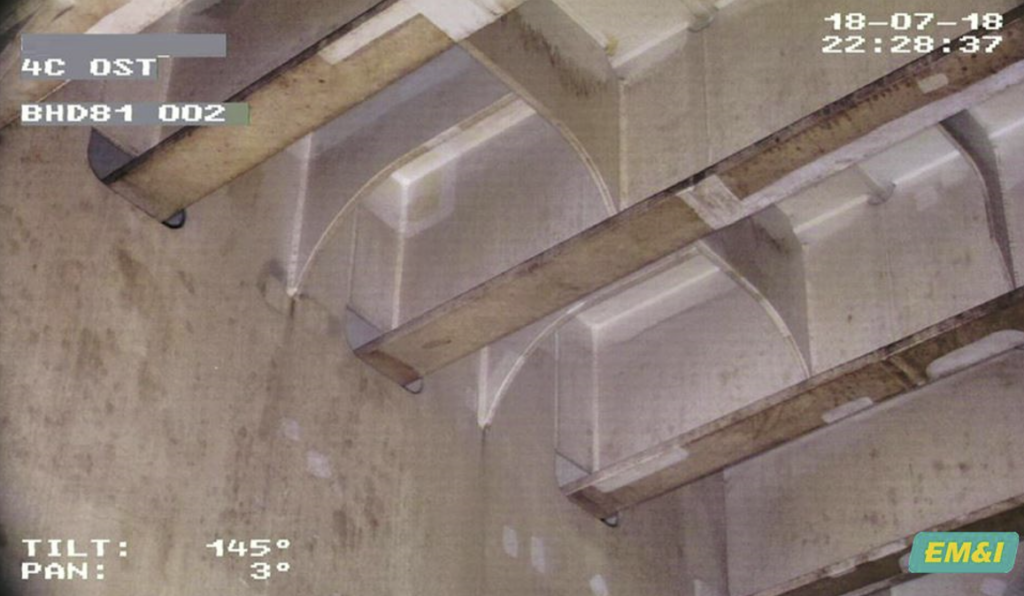
Safety, environmental, data and cost benefits
EM&I’s technologies are proven, class approved, and are designed to minimise safety risk, carbon emissions, cost, operational delays and POB (Persons on Board) – for example, a typical ODIN or NoMan team is made up of 2 to 3 people for a short duration rather than 10 or more used in traditional diver or rope access methods over longer durations.
Reducing exposure of large numbers of personnel to risk in confined spaces or underwater has clear safety benefits.
Equally, avoiding the environmental impact of transporting many personnel by helicopter or boat to offshore locations reduces carbon emissions.
Robotic inspections are already becoming even more ‘remote’ with live streaming of data to onshore surveyors and engineers are already available, leading to further safety, cost, and operational benefits. This also helps to reduce POB to a minimum and means that onshore specialists can direct the technical and operational work in a ‘low-cost low-risk’ environment.
Until recently only a small percentage of the data has been used to demonstrate regulatory or class compliance. This is changing fast – the ability to store, analyse and aggregate data and metadata is proving to be a great opportunity for being able to trend asset condition, plan remedial work and even improve design.
Independent report by Professor Andrew Woods of Cambridge University…
Several organisations including the HITS JIP have made great efforts to improve safety in this regard, encouraging improved processes and robotic, diverless, unmanned technologies.
As project leaders of this JIP, EM&I recently commissioned an independent study by Professor Andrew Woods of the BP Institute at Cambridge University to study and quantify the risk of fatalities in confined spaces, so that improved safety measures could be introduced.
The study suggests that our industry often operates below the generally tolerable levels of safety risk when working at height and in confined spaces, leading to several unfortunate and preventable fatalities.
It may be that shareholders, board directors and insurers are not aware of the level of safety required by regulators and courts and may believe that the latest procedures and equipment being used are adequate to mitigate or eliminate risks.
Boards should set specific targets for risk so that management who carry out risk assessments know what the target is and take the appropriate actions to meet or better these targets in order to protect life, corporate reputation, and value.
A risk of 1 in 1,000,000 is considered to be acceptable by most authorities, whereas anything below this needs to be justified as being ALARP (As Low As Reasonably Practicable) in other words that all has been done within reasonable limits to mitigate or eliminate the risk.
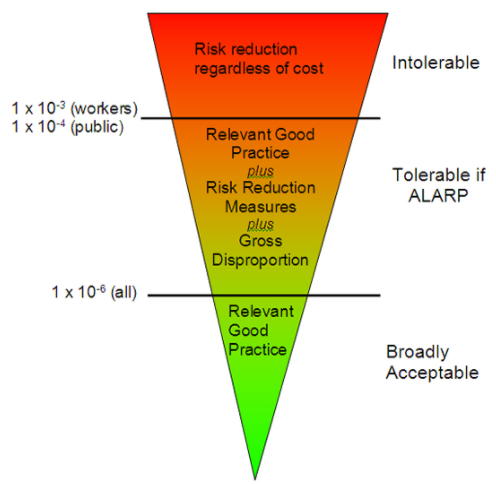
Professor Andrew Woods’ research has revealed that our industry operates significantly below the Broadly Acceptable levels of safety, with consequent concerns on reputation, costs, and legal challenges if senior managers knowingly allow work to be carried out when safer methods are available at reasonable cost, in other words ALARP.
Whilst these initiatives have made improvements, stakeholders need to be clear on the quantum of risk and importantly, how much should reasonably be spent to avoid confined space fatalities.
In 2020, HM Treasury in the United Kingdom assessed that the cost of an incident resulting in a fatality might be in the order of GBP 2 million (~US$2.75M). The ALARP principle, and regulatory guidance suggests that expenditure to mitigate the risk should be in ‘gross disproportion’ to the cost of an incident, maybe up to ten times the cost.
Case studies demonstrate the benefits…
Drillship off the coast of Angola
ODIN technology was used for critical valve inspections and repairs on a drillship operating off the coast of Angola, while the vessel was on hire, on station, and in operation. Twenty-one valves were inspected and three repaired, safely, on time, and at a fraction of the cost of conventional methods.
ODIN uses specially adapted cameras and manipulators, inserted through class approved ODIN access ports, installed adjacent to the valves to be inspected.
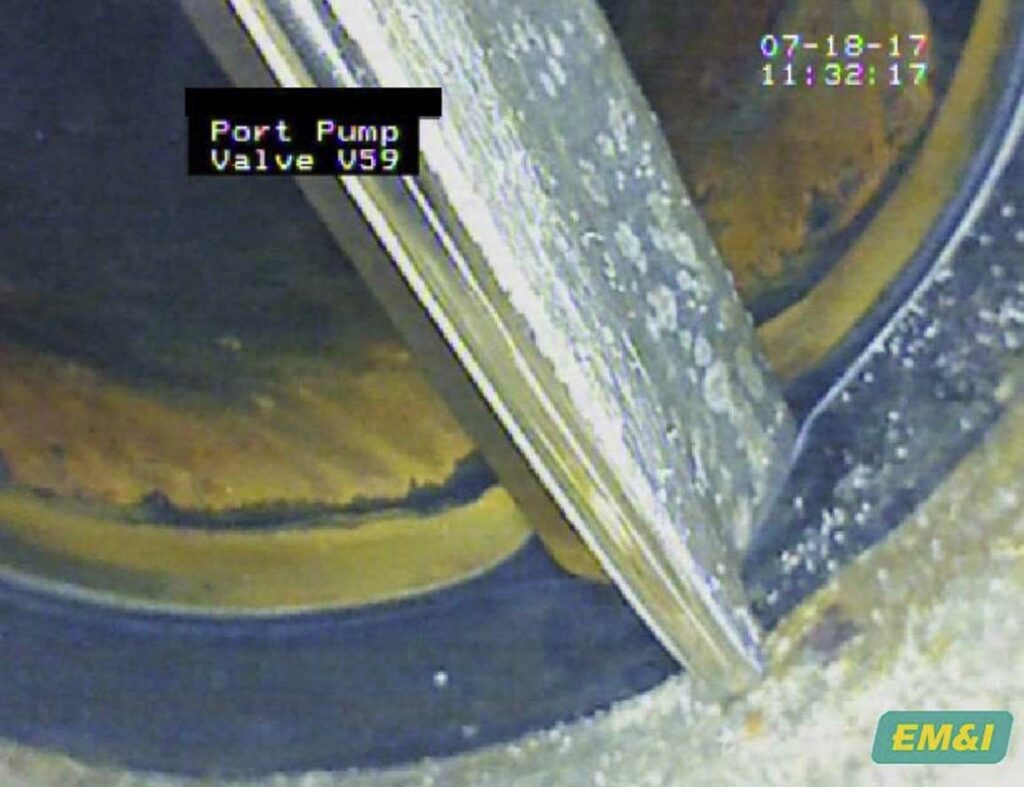
The ODIN repair technology was also used to isolate three valves that needed to be repaired using a double block inflatable bladder isolation system, inserted through ODIN access ports.
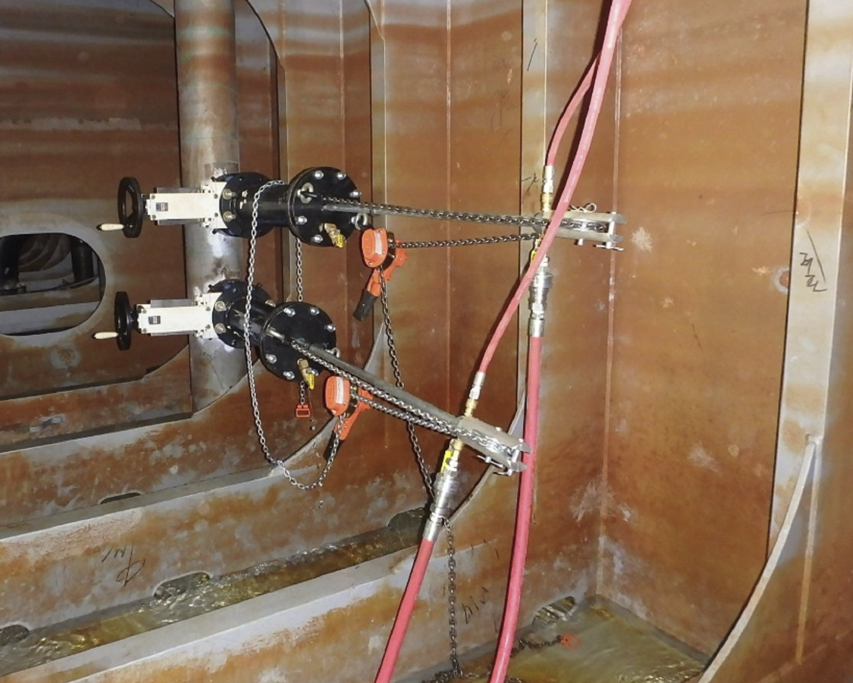
All the work was carried out without using divers and with no loss of uptime. Both the client and the class society were pleased with the results, with a 10/10 FPAL award (client feedback assessment system) for this project.
The benefits of using the ODIN system included avoiding the off-hire time of around 10 days that a dive team would entail, around a 50% cost reduction, and a 70% POB reduction.
A further benefit is that the ODIN access ports can also be used again for all subsequent valve inspections.
Semisubmersible operating off the coast of Malta.
A Bureau Veritas classified semisubmersible drilling rig, operating off the coast of Malta, needed to complete it’s 5-year periodic UWILD and carry out essential valve inspection, repair work and additional structural inspections whilst the asset was in operation and on hire.
The client chose to use EM&I’s advanced ‘ODIN’ technology, to avoid off-hire time, reduce costs, and enhance safety by eliminating diving operations.
The ‘ODIN’ diverless UWILD technology has now been proven on over 200 projects, on drillships, semisubmersibles, jack-ups, and FPSOs throughout the world with great success.
ODIN generates major cost and safety benefits for operators because the work can be carried out whilst the assets are on station and in operation. A POB (Persons on Board) reduction of around 70% leaves bed spaces available for other essential work, and because ODIN is not weather sensitive, it delivers high budget certainty.
ODIN was developed by EM&I and was encouraged by the influential HITS JIP whose membership includes the major class societies (ABS, LR, BV and DNV) and many of the world’s major operators and leasing organisations.
The innovative methods developed by EM&I are thoroughly tested and validated to demonstrate their compliance with class requirements. Areas inspected include the internal and in-service inspection of isolation valves using miniature cameras inserted into the adjacent pipework through specialised ODIN access ports.
Other areas include using specialised ROVs equipped with cavitation cleaners for cleaning sea chest inlet grids, bilge keels, mooring fairleads and thrusters, cameras and digital callipers for the inspection and measurement of mooring chain thickness, wear, and angles, as well as moonpool critical transition welds. In rougher sea states, or when ROVs cannot be used for operational reasons, the moonpool welds are inspected with the NoMan remote camera technology.
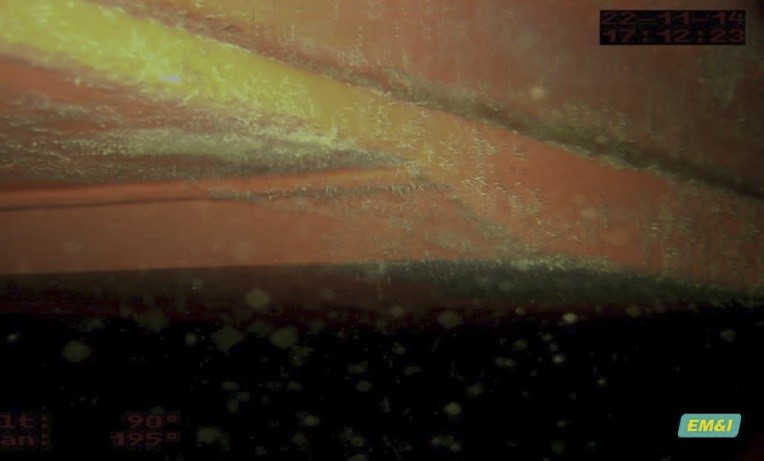
Inspection of confined spaces was achieved with minimal or no man entry, again using a combination of ROC (remotely operated cameras), laser scanning and advanced NDT methods.
The workscope on the asset was made up of four phases:
1. In-water cleaning and inspection of the pontoons, columns, and structures.
2. General visual and close visual inspection with thickness measurement of the internal structure of the columns, pontoons, topsides, and external structures.
3. Internal inspection and function test of critical isolation valves whilst in operation.
4. Replacement of a 10″ sea chest gate valve, with no down time or divers.
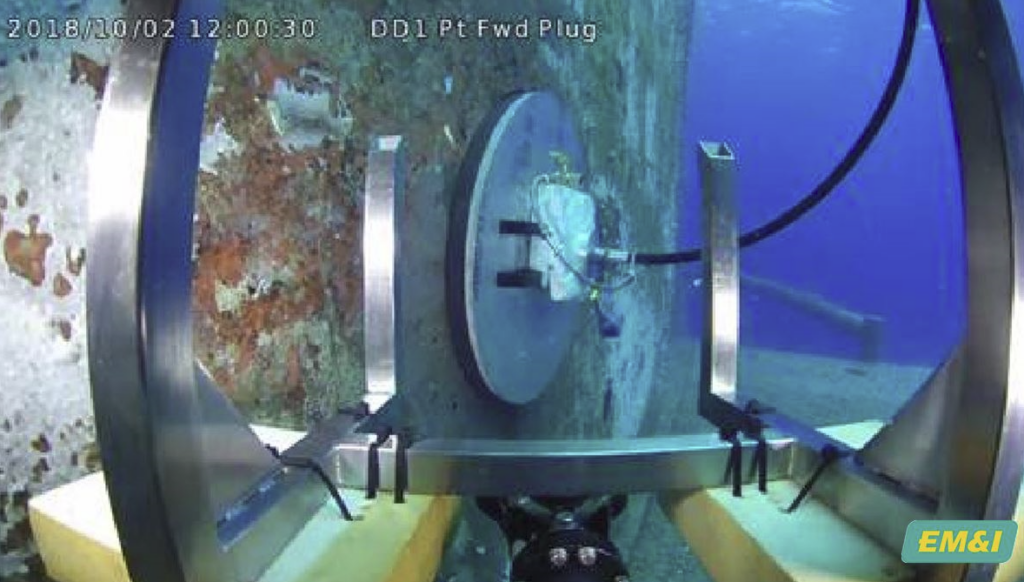
All the work was carried out whilst the asset was on station and in normal operation, with no downtime or loss of earnings.
The cost saving target for EM&I innovations was well in excess of 50%, and that in this case the class society were fully satisfied with the work, and the client awarded EM&I a 10/10 FPAL (the established client assessment system) rating for this project.
EM&I has also developed a number of other solutions such as HullGuard, a diverless retro-fittable ICCP system which gives long term protection of the hull, ExPert, remote non-intrusive inspection system for hazardous area electrical equipment, and BCT (Backscatter Computed Tomography), an NDT method for confirming condition of multi-layered components such as temporary repairs.